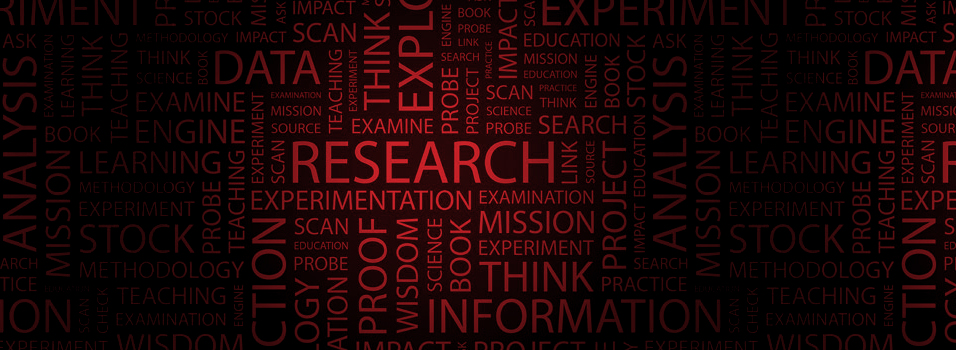
PROCESS CHEMOMETRICS
LABORATORY
@ CERES
Control Performance Assessment and Monitoring (CPA/CPM)
Most industrial processes contain hundreds or even thousands of control loops operating continuously in order to drive operations close to the designed target conditions, with low variability while guaranteeing the safety of plant personnel and equipments. Controllers are thus an intrinsic part of processes that collect information and produce actions at the level of manipulated variables, in an autonomous way, following some control law previously programmed and tuned according to the dynamic behaviour of the elements to be controlled. These control units are not peripheral elements but have indeed the capability of changing the overall dynamical characteristics of processes, playing a central role in key issues for the organizations, such as: product quality and variability (despite being often overlooked in process improving initiatives such as six-sigma), process efficiency (costs, machine operability), safety (some processes are inherently unstable and can only operated under well-tuned supervisory control), environmental impact and assets management. Control performance degradation can arise from a number of different sources, namely changes in the operation range (with associated modifications of the dynamic features of the process in open loop), variation in the products/materials/equipment being used, alterations in the status of the equipment (wear, fouling in heat exchangers surfaces, etc.), problems in actuators or final control elements (such as valve stiction or excessive friction problems), modifications in process disturbances (or load variables) and problems due to lack of maintenance. In this context, one can recognize that there are plenty of opportunities for control systems underperformance, and in fact, the average half-life period of “good” performance for a given control system, after its initial tuning, normally during the commissioning stage, is estimated to be of approximately 6 months. One should also note that even the assumption that control systems are indeed initially tuned properly is not necessarily true all the times, as quite often the controllers parameters are set too conservatively in order to guarantee a stable operation even without a foreseeable lack of maintenance in the future and/or because the task of tuning a large number of control loops is left to a few, very busy, process engineers, that hardly have the necessary time to tune each and every controller in an optimal way. Therefore, given the importance of control loops for the smooth operation of processes and the many factors that can lead to variability as well as degradation, it is quite natural that methodologies have been proposed and developments made regarding the assessment and monitoring of their performance, usually referred under the heading of Control Performance Assessment/Monitoring (CPA/CPM). In our group, we have developed a new historical-data benchmark index (IM), that is able to discern between perturbations in the system’s core modules, which are under the supervision of process owners, from those originated at the level of disturbances, usually involving other stake-holders. It is a generalization of the current data-driven index (Iν) as it can be shown that it reduces to this index for the particular case where the variability of the disturbances is the same in the reference or benchmark period and in the monitoring period.